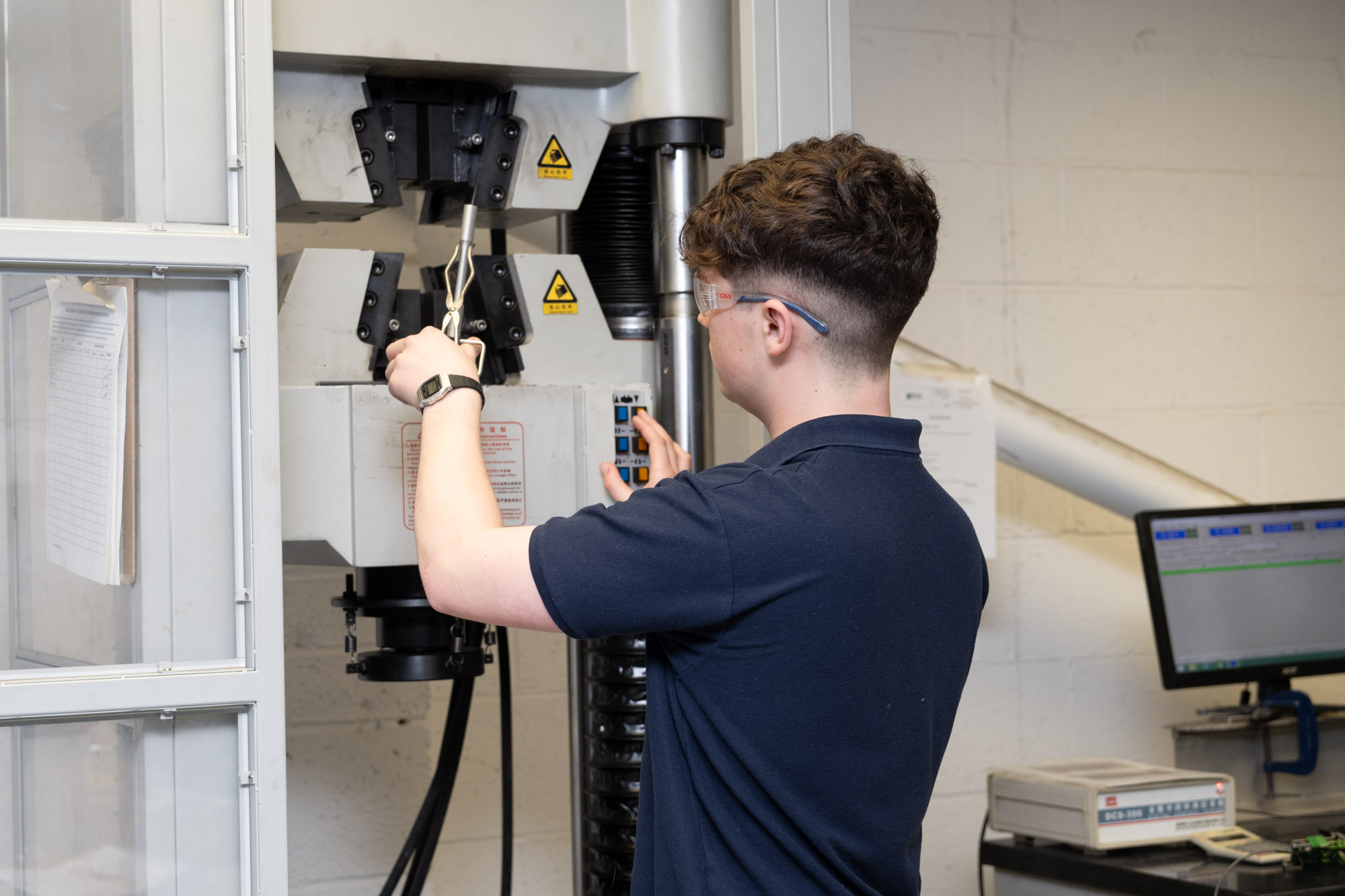
Advanced Testing for Welded Structures in the UK
At LTi Metaltech, we specialise in both destructive and non-destructive testing to ensure the integrity of welded structures. Our cutting‐edge technology and rigorous quality assurance protocols guarantee that every component meets the highest standards, even under challenging vacuum, pressure, and temperature differentials. This comprehensive testing approach is central to our reputation as recognised experts in the fabrication and manufacture of high integrity welded structures across the UK.
Our Non-Destructive Testing Services:
Our non-destructive testing (NDT) methods are designed to evaluate the performance of welded structures without causing damage. We offer a wide range of NDT services, including:
• Radiography (analogue & digital): Advanced imaging for detailed weld inspection.
• Dye penetrant testing (PCN Level II): A proven method to detect surface-breaking defects.
• Helium leak testing: Ensuring airtight welds for critical applications.
• Hydrostatic testing: Validating pressure integrity under realistic conditions.
• High vacuum testing: Confirming performance in low-pressure environments.
• Visual weld examination (CSWIP 3.1): Thorough assessment by certified inspectors.
• Dimensional evaluation (Faro): Precise measurement techniques for weld accuracy.
• Functional testing: Verifying that every weld meets its intended performance criteria.
These techniques enable us to deliver reliable testing of the integrity of welded structures, ensuring safety and compliance with industry standards throughout the UK.
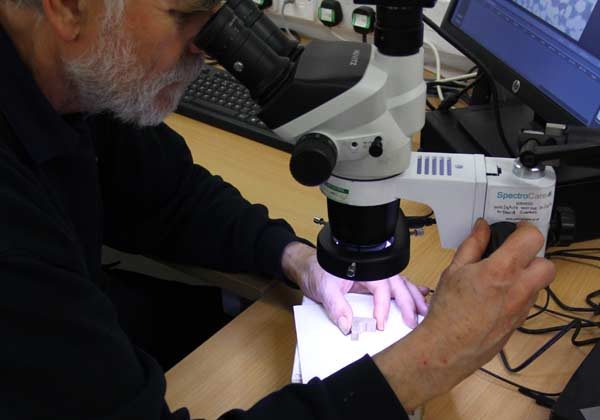
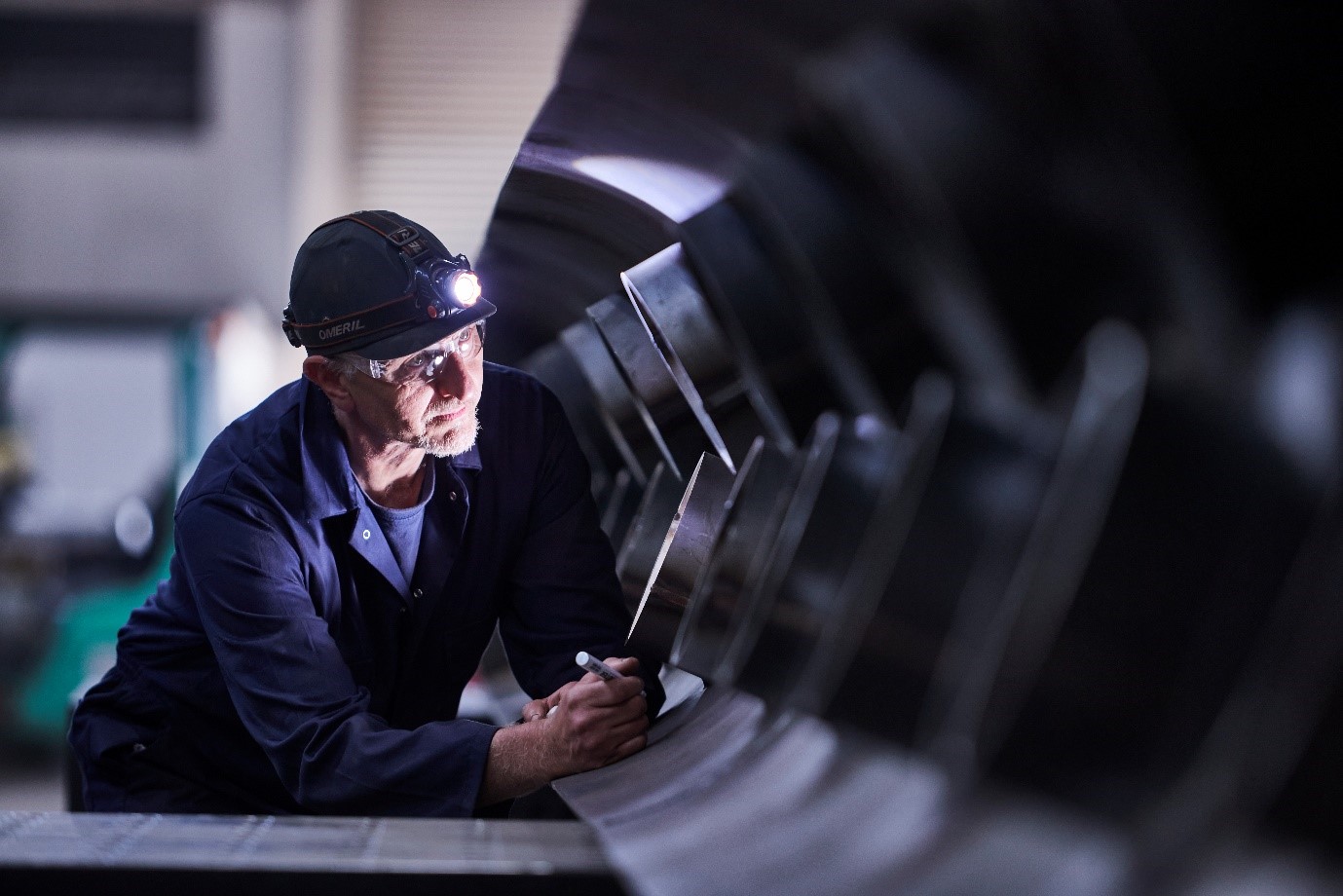
Comprehensive Destructive Testing Methods:
For a complete understanding of material performance, our destructive testing procedures subject welded structures to controlled stress and strain. Our destructive testing portfolio includes:
• Tensile Testing: Assessing strength and ductility.
• Impact Testing: Determining toughness and fracture resistance.
• Bend Testing: Evaluating weld flexibility and durability.
• Fracture Testing: Analysing crack propagation under stress.
• Macro/Micro Examination: Detailed inspection of weld quality.
• Hardness Testing: Measuring material resistance and integrity.
These tests are essential for validating the structural performance and safety of our welded assemblies, ensuring they are fit for purpose under extreme conditions.
Commitment to Quality and Certification
At LTi Metaltech, quality assurance is our prime concern. All of our coded welding procedures are:
• Validated by qualified welding inspectors
• Approved by an independent third party
This rigorous certification process reinforces our commitment to delivering the highest standards in both destructive and non-destructive testing.


Why Choose LTi Metaltech for Welded Structure Testing?
• Expertise in Testing: With decades of experience in both destructive and non-destructive testing, we provide reliable assessments that meet international standards.
• Innovative Technology: We use the latest equipment, from digital radiography to precision measurement tools (Faro), to ensure accuracy.
• UK-Based Excellence: Proudly serving the UK market, our solutions are tailored to the specific demands of local industries and environmental conditions.
• Safety & Compliance: Our methods ensure that every welded structure can withstand demanding operational pressures and temperature differentials.
Whether you require detailed non-destructive examinations or comprehensive destructive testing, LTi Metaltech is your trusted partner for testing the integrity of welded structures in the UK.