West Technology – Meeting DFM Challenges
As a longstanding specialist in the fabrication and welding of high-end pressure vessel structures, LTi Metaltech was tasked by their customer West Technology, with manufacturing a chamber pot pressure vessel with the capability to withstand both positive and negative pressures.
The vessel itself was designed to be used by West Technology’s end customer Megger, for the impregnation of electrical windings in one of their high-voltage testing machines.
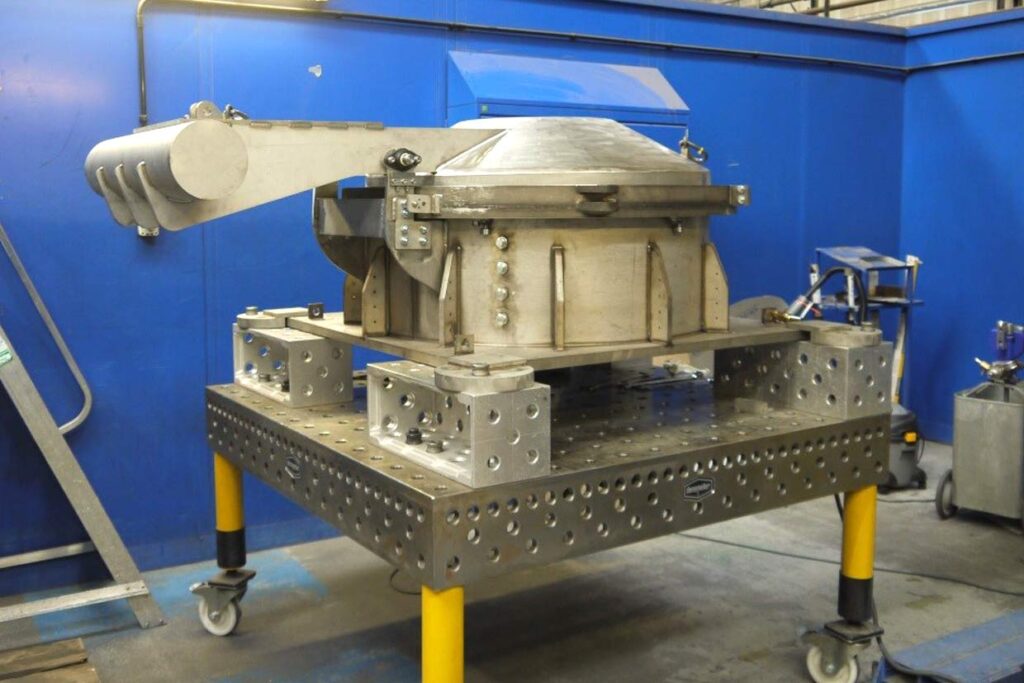
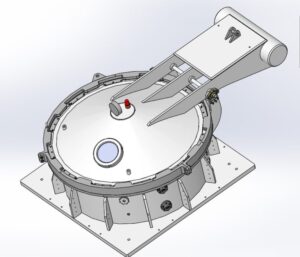
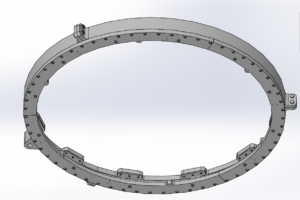
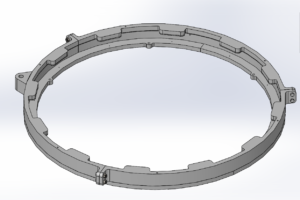
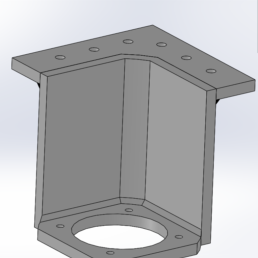
The Challenge
In this project, LTi needed to identify new ways of improving the structure’s manufacturability, so they could meet their customer’s requirement for a reduced cost price point. LTi quickly recognised that they would need to make a series of radical changes to their customer’s original design specifications, if they were to resolve both of these challenges in alignment with the customer’s requirements.
There were many elements in the vessel’s original design specifications that presented LTi with challenges:
Firstly, a number of its major parts had been designed to be manufactured from large billets of stainless steel, which would be both labour intensive & expensive to achieve their required finished state.
(This together with the extra complexity of some of West Technology’s original designs can be seen in the diagrams on the left)
Secondly, the chamber pot’s counter weight was originally designed to be made out of a single bar of stainless steel with a mass of 115kg – an expensive option given other alternatives which could have been found. (West Technology’s original design for the chamber pot’s counter weight and removable hinge bracket can be seen on the right )
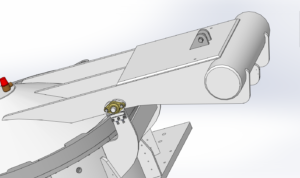
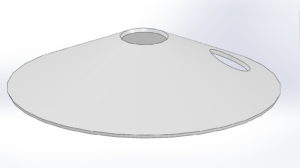
The original designs also posed some geometric challenges; most notably the cone top structure on the lid of the chamber pot, which in its original state would have been expensive for LTi to manufacture with their existing tooling capabilities. (The diameter hole on the cone top structure was previously a lot smaller, which can be clearly seen in the original West Tech design below)
Consequently, LTi would need to be extremely innovative to achieve the required Design for Manufacture changes necessary to improve the vessel’s manufacturability and reduce the total cost of producing it.
How LTi went about it
Following from detailed review of all aspects of both the original design stages and the related manufacturing processes, LTi’s expert team of innovative designers and manufacturers utilized techniques including 3D modelling to identify design and structural changes which would make the vessel more cost effective to produce.
Working to EN 13445 European Pressure Vessel Standards, which sets the minimum quality standards in the design, fabrication and inspection of vessels; LTi made a number of key changes:
Drawing on their extensive welding expertise, LTi reworked the design of major parts previously configured to be manufactured from large billets of stainless steel into welded structures that only required limited welding or finish machining. (Some of LTi’s design changes are illustrated in the diagrams on the right).

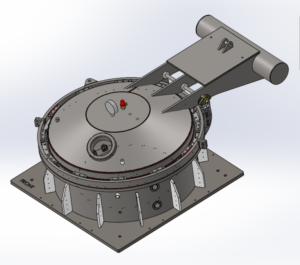
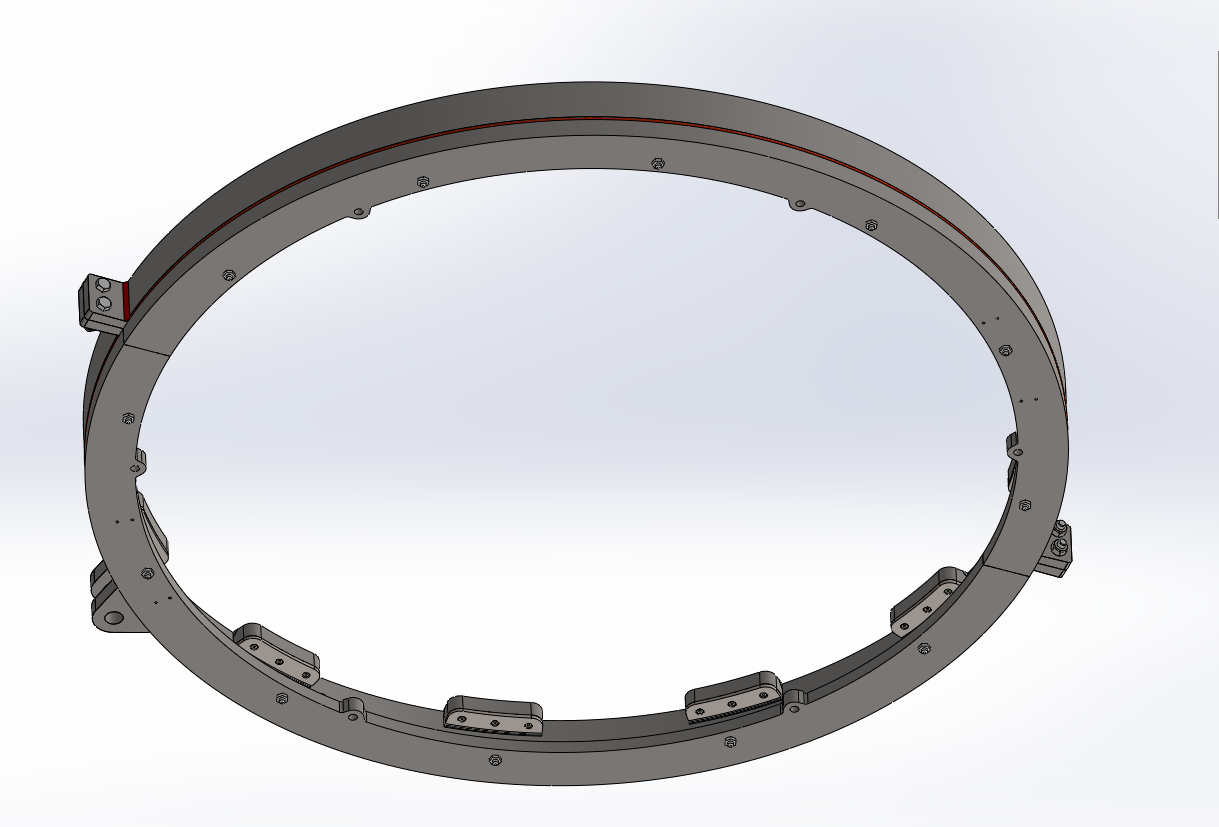
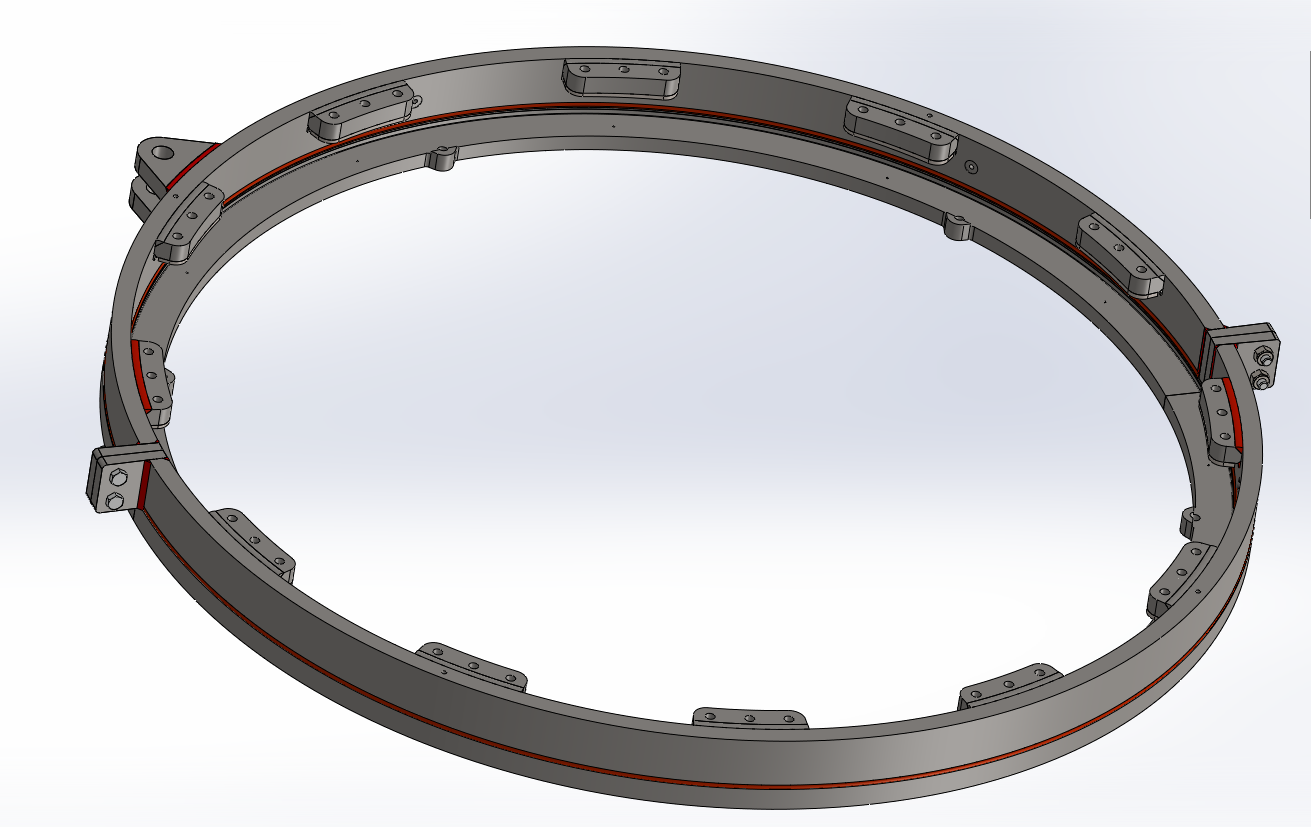
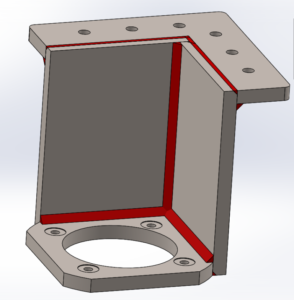
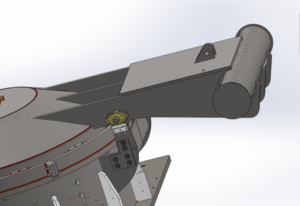
LTi also altered the chamber pot’s counter weight to a tube design consisting of inserted circular blocks cut from what would otherwise have been scrap metal offcuts. This helped to significantly reduce costs and made the assembly safer. (The changes LTi made can be clearly seen in diagram, outlined on the left)
The design geometrics of the lid’s cone top structure was also revised to better suit LTi’s tooling capability. By increasing the cone top’s diameter hole by a factor of two, it was now able to be rolled out much more cost effectively on a standard rolling machine – saving approximately £1000 for this part alone. (The cone top’s larger diameter hole is clearly visible in LTi’s revised design on the right)
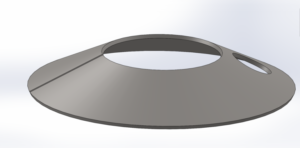
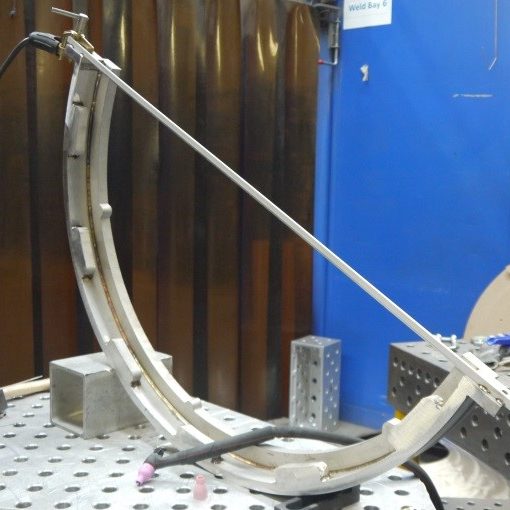
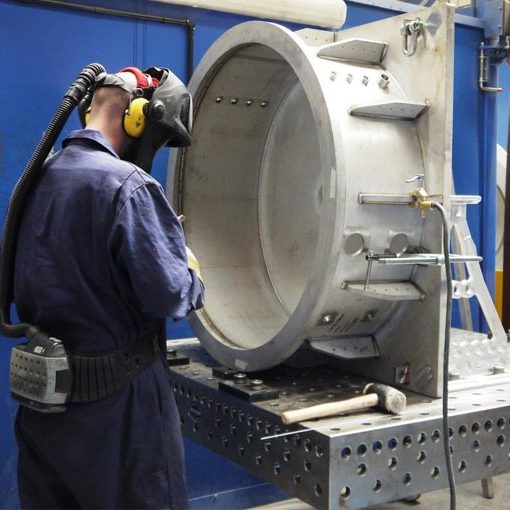
These changes allowed LTi to reduce the total amount of assembly hardware required to fabricate the multiplicity of machined parts. Essentially this reduces the number of assembly steps involved, which further lowers the risk of any potential human errors and subsequent rework which can slow down the manufacture of a structure and push up costs.
What was the outcome?
LTi successfully met all the required design changes they set out to achieve, improving the manufacturability of the chamber pot and giving their customer a much more cost effective to produce structure that was still fit for purpose.